Early Factories Were Dangerous
Folks, let’s talk about the perils of those early factories. Back in the day, the Industrial Revolution brought about a revolution in productivity thanks to all the newfangled machinery, energy, and factories reorganizing the way work was done. But along with all those gains in GDP and wages came new risks that nobody was prepared for.
Now, don’t get me wrong. The pre-industrial world had its fair share of dangerous jobs too, like coal mining, blast furnace tending, and working the high seas. And even a blacksmith’s shop had its hazards, what with all the sharp tools and hot metal flying around. But the industrial factories brought a whole new level of danger.
These machines had blades and gears exposed, just waiting to catch a finger or a hand. And the woodworking machines were especially treacherous, especially those joiners. Power tools were powered by belts, shafts, and flywheels with no guardrails in sight. Walkways and ladders were high above the factory floor with no railings to keep you safe. Cranes could knock you out cold or drop heavy materials on top of you. Steam engines had boilers that could explode. High-voltage wires posed a real threat of electrocution. Smelting furnaces could break out with hot metal. And toxic gases could asphyxiate a man in a heartbeat. Workers lost fingers, eyes, limbs, and even their lives to these hazards.
The more power you put into those factories, the higher the productivity, but also the higher the injury rate. The faster and heavier the equipment was moving, the more dangerous it became. Safety historian Mark Aldrich found that in the US from 1869 to 1927, every 1 horsepower per worker was associated with a 3% increase in the injury rate.
Now, we don’t have a lot of solid numbers on accidents before the early 1900s, but there’s plenty of evidence that the injury rate was higher in 19th-century factories than in traditional workshops. In 1910, the New York State Compensation Commission wrote that “before machinery was introduced into modern industry, industrial accidents were relatively few and unimportant.” And in 1913, Leslie Robertson of the Ford Motor Company said that “the element of injury has been ever present in an increasing ratio as modern development and methods have been utilized.”
Systems Thinking – What’s That?
Let’s talk about a problem that was at the root of all the trouble in those early factories – a lack of thinking about safety as a system. Both workers and management had the wrong attitude when it came to safety. They thought that each individual worker was responsible for their own safety and nobody saw it as the job of management to provide a safe working environment.
Now, part of this was just how things were done back in the day when everyone was a craftsman working with hand tools. But in a factory with heavy machinery, one person’s actions could put everyone else at risk. And that’s how you got accidents happening, like someone starting up a machine without realizing a repairman was working on it, or someone moving a car along the rails without realizing someone was under it.
Back then, people just saw work as inherently risky, just like life was inherently risky. Sailors could get lost at sea, farmers could suffer from drought or disease, and anyone could catch a deadly illness at any time. On-the-job accidents were just part of the deal.
So, when accidents happened, people just blamed the worker for being careless. But that was just the tip of the iceberg. They didn’t look at the root causes and how to fix them. They didn’t have what we call “systems thinking” today.
And because they didn’t recognize the role of the work environment in safety, they just saw accidents as inevitable. They didn’t understand how to use statistics to reduce risk, or how to exercise agency to prevent accidents from happening.
This mentality was reflected in the laws of the time. If you got hurt on the job, it was hard to get compensation from your employer. Your only option was a lawsuit, which was expensive and often not worth it. Employers had all sorts of ways to escape liability. If you were even a little bit at fault, they could say it was your own fault. If another worker’s negligence caused your injury, the employer wasn’t liable. And if the accident was just part of the job, the employer wasn’t liable either. These defenses were known as the “unholy trinity” and because of them, it’s estimated that only one in eight workers received compensation after a lawsuit.
Attitudes Change
Next, let’s talk about a shift that happened in the late 19th century when it came to workplace safety in factories. There were a bunch of social reform movements trying to fix the problems, like ending child labor and working to reduce the number of hours people were working.
In the US, the issue of workplace safety was thoroughly investigated in a report called “Work-Accidents and the Law” by Crystal Eastman. She looked at every single fatality and hospitalization in one county over a year and talked to workers, foremen, and families to understand what was going on. She found that accidents were not happening because workers were careless, but because there weren’t enough safety provisions, inspections, warning systems, and training. And the long hours and fast pace of work in the factories were also contributing to the problem.
Another writer, William Hard, wrote an article called “Making Steel and Killing Men” that asked whether we had to keep paying the price of all the accidents in order to be leaders in the production of steel. Several states set up commissions to study the issue and they agreed that there was a serious problem.
The reformers came up with different solutions, like requiring public reports on accidents or granting supervisory power to public inspectors. But the key change that happened was a new system of liability called “workmen’s compensation”. This was a “no-fault” system where the employer was always liable for an injury on the job. The worker would get a payment based on their injury, but they wouldn’t be able to sue for more. This system was first enacted in Germany in 1884, in Britain in 1897, and then in the US state by state in the 1910s.
This new system was good for both employers and workers. Workers got automatic compensation and both sides avoided expensive lawsuits. The system was more predictable and efficient, with less money going to lawyers and more going to accident victims and their families.
But the new system also dramatically increased employers’ costs. The cost of a fatal accident went from a few hundred dollars to a few thousand dollars, and insurance premiums increased as much as five times. But the best part was that the no-fault nature of the system shifted the focus from fighting liability in lawsuits to preventing injuries. Companies started setting up safety departments staffed by engineers, and safety engineering became its own subdiscipline. These engineers saw it as their professional duty to reduce injury rates and believed that almost all accidents could be avoided with the right tools, environment, and training.
Safety Engineering
Back in the day, safety in the workplace was not a priority. Sure, people had dangerous jobs like coal mining or working at the blast furnace, but the introduction of factories brought a whole new set of risks. Machines had exposed blades, high-pressure boilers, and even toxic gases that put workers in harm’s way. But as time went on, a movement for workplace safety began to take shape.
That’s where the safety engineers came in. They started to tackle the root causes of injuries head-on. They put guards around moving parts of machines, invented locks so machines couldn’t be turned on without them, and made automatic shutoff mechanisms. They even added railings on walkways and improved lighting to make it easier to see hazards. But it wasn’t just about the equipment. The workers needed education and training too. Companies launched propaganda campaigns, held safety contests, and even established on-site medical care. The earliest recorded instance of a company providing medical care for their workers was when industrial nurse, Phillipa Flowerday, was hired by the firm of J. & J. Colman in Norwich, Great Britain. Such a practice later became standard in U.S. industry, and, in 1914, Ford established a medical department in his factory with a full-time physician and nurse to provide medical care for his workers, and it became common for companies like the Ford Motor Company to provide onsite medical care for their factory workers.
All of this hard work paid off. The injury rates in many US industries dropped dramatically in the early 1900s. And it’s all thanks to the safety engineers, insurance companies, and everyone who recognized the importance of creating a safe working environment.
Safety Wasn’t Something Average Workers Cared About
Back in the day, safety wasn’t exactly at the forefront of the average worker’s mind. It was something that was driven by management and those in positions of power.
In fact, when you look at the numbers, safety just wasn’t a big concern for workers. During all those strikes that happened in the late 1800s, most of ’em were about better pay, not about safety. And when new safety measures were introduced, workers were often resistant to them. They saw the daily inconvenience, like guards on machines or uncomfortable safety gear, and didn’t always understand the importance of avoiding rare disasters.
Now, it wasn’t just the workers who were resistant to change. Smaller companies were often less likely to invest in safety departments and programs, since their insurance premiums didn’t necessarily reflect their safety record. It was the big companies, like US Steel and DuPont, that were leading the charge on workplace safety. They had the resources and visibility to make a difference, and they knew they had a lot to lose from a bad reputation.
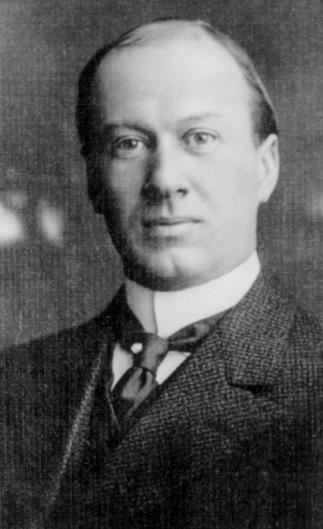
E.I. du Pont
A note about Dupont: DuPont, a company well known for its commitment to safety, started as a gunpowder manufacturer in 1802. The founder, E.I. du Pont, was deeply committed to safety and implemented the first written safety rules in 1811, which included strict regulations for employee behavior and immediate dismissal for anyone who showed up for work intoxicated. Despite explosions in 1815 and 1818 that killed 45 people, the company provided free housing and lifetime pensions to widows and dependents of deceased workers. In the mid-1800s, Lammot du Pont developed machinery to mechanize processes, making work safer. The company evolved into a chemical processing company and developed a formal safety program and hired its first full-time physician. The “Safety First” program in 1911 was launched with workers’ safety committees, safety literature, and rallies, which led to DuPont being recognized as a source of safety information, resources, and practices for companies worldwide. In 1912, the US National Safety Council was created and DuPont’s frequency rate of major injuries per million hours worked dropped from 43.2 in 1912 to 3.4 in 1927, reflecting the importance of safety in the company.
All in all, it seems like the average person has a hard time thinking about risk and the importance of safety. It just doesn’t come naturally. So it’s up to those in positions of leadership to drive the change and implement the training and education needed to make a safer workplace.
And who knows, maybe we can learn something from the past and make sure that everyone, from the top down, is always thinking about safety in the workplace.
Liability Laws Were Very Effective
Let me tell you about the magic of li’l old liability law. Ain’t it amazing how a small tweak to the rules can set off a chain reaction of management and engineering decisions that end up creating a whole new safety culture. It’s a classic example of economics at work – just put a price on the harm, internalize the externality, and let the market do the rest.
Now, I gotta be honest, the reason workers’ comp had such a big impact on factory safety is because the previous regulations just weren’t cuttin’ it. Part of the problem was lack of enforcement, and part of it was because manufacturers could often get off the hook with juries of their peers. But those difficulties just make the beauty of the liability solution even more apparent. Liability law eliminated trials and the insurance companies provided funding for inspectors. It’s hard to imagine a better outcome coming from direct regulation or micromanagement by the government.
And, on a related note, it’s fascinating how different approaches to safety regulations in different countries can lead to different outcomes. Europe started with strict machine guarding requirements, which made employers focus on following the law rather than preventing injuries. Meanwhile, in the US, ineffective early state legislation combined with the spread of workers’ comp led businesses to view safety in business terms and seek out cost-effective ways to prevent injuries.
Another important lesson is that the details of the law matter. In theory, employers were always liable for injuries, but the old law wasn’t enough of a deterrent and made it too hard for workers to seek compensation. Workers’ comp simplified and streamlined the process, making it more likely that workers would actually get compensation. It turns out that predictability and low overhead are more important than determining fault accurately. It makes me question any system where individuals have to file a lawsuit to receive compensation.
The effectiveness of this system has me thinking – what if we applied a similar model to other areas, like medical malpractice? What if we got rid of lawsuits and instead had a no-fault system where medical providers always pay for any complications under their care? It might shift the focus from avoiding liability and following rules, to actually preventing medical accidents in the most effective and efficient way possible.
Conclusion
The early factories of the Industrial Revolution posed a new level of danger to workers, who were not prepared for the risks associated with the new machinery, energy, and factories. Power tools, steam engines, and toxic gases were just some of the hazards that workers faced. The faster and heavier the equipment, the higher the injury rate. The lack of thinking about safety as a system was at the root of the problem. Workers and management thought that each individual was responsible for their own safety and didn’t understand the role of the work environment in safety. The pre-industrial world had its share of dangerous jobs, but the industrial factories brought a new level of danger.
In the late 19th century, there was a shift in attitudes towards workplace safety in factories. Reformers investigated the issue and found that accidents were happening due to a lack of safety provisions, inspections, warning systems, and training. The reformers introduced a new system of liability called “workmen’s compensation” that was a “no-fault” system where the employer was always liable for an injury on the job. This new system dramatically increased the cost of employers but also shifted the focus from fighting liability in lawsuits to preventing injuries. Companies started setting up safety departments staffed by engineers and safety engineering became its own subdiscipline. The injury rates in many US industries dropped dramatically in the early 1900s, thanks to the hard work of safety engineers, insurance companies, and everyone who recognized the importance of creating a safe working environment. The average worker didn’t care about safety, and it was driven by management and those in positions of power. The liability laws were very effective and eliminated trials, making it more likely that workers would receive compensation. The system has led to the development of a safety culture in the workplace.
In conclusion, the early factories were a dangerous place to work in, but through the efforts of social reformers, safety engineers, and liability laws, the workplace became a safer environment for workers. The shift from individual responsibility for safety to a collective responsibility of employers to provide a safe working environment was crucial in reducing the number of workplace accidents and injuries. The implementation of workers’ compensation and the development of a safety culture in companies have made a significant impact on the well-being of workers and continue to be a model for other industries to follow. The story of workplace safety is a testament to the power of collective action and the positive outcomes that can be achieved when people come together to make a difference.
References:
The bulk of the historical account in this article is based upon Mark Aldrich’s renowned book, Safety First. Mark Aldrich is an economist and also an OSHA researcher.
- Aldrich, Mark. Safety First: Technology, Labor, and Business in the Building of American Work Safety, 1870-1939. 1997.
- Eastman, Crystal. Work-Accidents and the Law. 1910.
- Hard, William. “Making Steel and Killing Men.” In Injured in the Course of Duty, 1910.
- https://www.dupont.com/news/safety-at-our-core.html